製紙および段ボール工業におけるでん粉の利用
最終更新日:2014年10月10日
製紙および段ボール工業におけるでん粉の利用
2014年10月
王子コーンスターチ株式会社 北海道工場 工場長 砂田 美和
【要約】
製紙産業では、でん粉は、主に増粘剤、テクスチャー改良剤や打ち粉として使用される食品用とは違い、紙の強度向上剤および接着剤として、また、段ボール産業では接着剤として利用されており、その使用方法はでん粉の性質をうまく利用した巧みなものである。
はじめに
日本では、食品以外にも各種工業製品にでん粉が利用されており、その中でも製紙産業と段ボール産業がその大半を占めている。そこで本稿では、製紙と段ボールにおけるでん粉の使用目的およびその使用方法を中心に紹介する。
1. 製紙産業におけるでん粉の利用
製紙において、でん粉を利用する目的は、主に紙の乾燥強度を向上させ、印刷、加工および包装に対する適性を改善させることにある。紙の品質は原料であるパルプに大きく影響されるが、昨今では古紙使用比率が増えてきており、原料の品質低下を、補強剤としてでん粉を使用することで補うことが多くなっている。以下にでん粉がどのように利用されるのか、紹介する。
(1)製紙工程概略
まず木材のチップに薬液を加え、高温・高圧で煮て、チップ中の樹脂を溶かし、繊維分だけを取り出して、漂白することで紙の原料となるパルプを製造する(パルプ化工程)。次にパルプを目的とする紙に適した長さ、ほぐれ具合にして、でん粉を含む薬品を添加する工程(調成工程)を経て、水に分散したパルプをワイヤーに乗せ、ある程度まで脱水、シートを形成、ロールの間を通してさらに脱水後、乾燥、巻き取りを行って(抄紙(しょうし)工程:図1)、紙は出来上がる。また必要に応じて、紙の上に美しい印刷が出来るように顔料を塗る工程(塗工工程)を経る場合もある。板紙(厚紙)は、抄(す)き上げて乾燥する前のパルプシート(湿紙)に、別に抄いたパルプシートを2〜8枚重ね合わせることで製造されている。
(2)内添用でん粉
製紙における初期工程で、脱水前のパルプ懸濁(けんだく)液の状態で各種薬品を加えることを内添と呼び、内添用でん粉もここで添加される。でん粉の役割は、主にパルプ繊維とパルプ繊維の接着剤であり、最終的に出来上がる紙の強度を向上させる。またでん粉は、微細繊維や填料(てんりょう)(紙に抄き込まれる炭酸カルシウムなどの鉱物)の歩留まり向上、後工程のワイヤー上での脱水性向上にも寄与する。
パルプ繊維はアニオン(陰イオン)性であり、填料などもアニオン性のものが多いことから、パルプ繊維や填料との親和性を上げるために、でん粉はカチオン(陽イオン)性の方が望ましく、一般的にカチオン化でん粉または両性化でん粉が利用される。カチオン化でん粉は、でん粉の水酸基に三級アミンまたは四級アンモニウム化合物を付加させたものであり、パルプ懸濁液に添加する時は一般的にあらかじめ糊化(こか)させておく。ただし、ほぼ同じ機能を持つポリアクリルアミドに代表される化成品に代替されつつあり、内添用でん粉の使用量は漸減傾向にある。
(3)スプレー用でん粉
スプレー用でん粉は使われ方によって層間用と表面用に分けられる。層間用は板紙の紙と紙との接着剤として使用され(図2)、でん粉スラリーのまま(糊化させずに)、湿紙と湿紙の間に文字通りスプレーされ、後工程のドライヤーパートで加熱されることにより糊化が起こり、でん粉が接着剤として機能する仕組みになっている。このような使われ方のため、使用されるでん粉はドライヤーパートの性能(条件)によって異なり、でん粉が十分糊化しやすい条件(水分が多く、温度が高いなど)であれば未加工のでん粉でも問題ないが、糊化しづらい条件(水分が少ない、温度が低いなど)の場合、糊化しやすい(糊化温度が低く、若干粘度が低いなど)でん粉が必要となり、アセチル化でん粉、尿素リン酸化でん粉などが使用される。また使用目的からスプレーしたでん粉は紙表面にとどまっていることが大切で、中に浸み込んでしまっては接着機能が果たせないため、粒子が大きいばれいしょでん粉を好んで使用する製紙メーカーもある。
表面用は通常の一枚紙においてプレスパート上で、でん粉スラリーを上からスプレーする方法であり、目的は内添用とほぼ同じで、紙の強度を上げたい場合に採用される。使用されるでん粉は層間用とほぼ同じである。
(4)サイズプレス用でん粉
商業印刷では粘度の高いインキが使用される場合が多く、印刷時、紙の表面はインキのタックによって引っ張られ大きな負荷がかかるため、表面強度を上げる目的ででん粉などを紙の表面に塗布することが行われ、この工程を「サイズプレス」と呼ぶ。
サイズプレスはドライヤーパートの中間に設置されており、2本ロールタイプ(図3)、ゲートロールタイプ(図4)などがある。2本ロールタイプはロールの間にでん粉糊の液だめを作り、その中を一端乾燥した紙を通して塗布する。
ゲートロールタイプは糊液をロールに転写させて紙に塗布する。よってサイズプレス後は再湿するため、再度乾燥させる必要がある。またサイズプレスは高速かつ紙の表面に均一に塗布しなければならないため、サイズプレスに使用されるでん粉は粘度が低いものでなければならない。従って、現在はあらかじめ低粘度化処理された酸化でん粉が多く使用されているが、最近は未加工または低加工度のでん粉を使用して製紙工場内で低粘度化を行う自家変性システムによる自家変性でん粉が多くなってきている。
酸化でん粉は低分子化と共にカルボキシ基、カルボニル基の生成が起きているため、老化が起きづらく使い勝手が良いでん粉である。サイズプレスはその装置の特性上でん粉糊液の一部は系内を循環するため、酸化でん粉糊液の経時安定性の高さは紙品質の安定性にもつながっている。
自家変性システムは酵素変性方式と熱化学変性方式の2タイプがあるが、現在は酵素変性方式が多い。酵素変性はα−アミラーゼをでん粉スラリーに添加しておき、バッチクッカーでゆっくり加熱することで糊化と低粘度化を同時に行う方式で、使用されるでん粉は未加工のコーンスターチ、低加工のタピオカでん粉が多い。ただし酵素変性でん粉はα−アミラーゼで単純に加水分解しているだけなので、糊液の安定性が悪く、使い勝手も良くないため、紙品質を維持するのに苦労があるが、安価であることから昨今はこの方式が増えている。
(5)塗工用でん粉
カレンダーやカタログ雑誌などの紙は、表面がツルツル、艶々(つやつや)して見た目も印刷写りも非常に良いもので、一般的に塗工紙と呼ばれている。塗工紙の表面には無機顔料(炭酸カルシウムなど)が塗られており、これらの顔料を紙の表面に付着させるために接着剤としてでん粉やラテックスなどの水溶性バインダーが使用される。
紙に塗布する前の顔料やバインダー、その他の薬品(耐水化剤、滑剤(かつざい)など)を混合した塗料をコーティングカラーと呼び、このカラーに使用されるバインダーは紙に塗布した時に顔料の表面を十分カバーし、接着のために、ある程度原紙に浸透する必要がある。また一般に接着力という点では水溶性バインダーの中ではでん粉系が最も弱いが、バインダーに求められる機能は接着力だけではなく、コーティングカラーの流動性、粘性、保水性および乾燥後の表面の仕上がり特性なども求められるため、必要に応じて複数のバインダーが併用される場合が多い。従来はでん粉が主、ラテックスが従であったが、ラテックスの品質向上に伴い、最近はラテックスが主体となっている。ただしでん粉にはラテックスにはない機能(保水性など)があり、全く無くすわけにはいかない場合が多い。コーティングカラーはかなり高濃度にする必要があることから、でん粉も低粘度にする必要性があり、サイズプレス同様、酸化でん粉が最もよく使用されるが、顔料との相性が良く、カラー特性、塗工紙の印刷適性も良い尿素リン酸化でん粉もよく用いられる。また品質的には若干落ちるものの、塗工紙の競争力強化のために、コスト削減対策として自家変性でん粉も使用されるケースが増えている。
2. 段ボール産業におけるでん粉の利用
段ボールは目にする機会が多く、包装にもよく使用されているなじみがある包装資材である。構造は単純で波状に加工された板紙を両外側二枚の板紙に挟んで接着しただけものである。この内側の波状の板紙を中芯、両外側の板紙をライナーと呼び、中芯とライナーを接着しているのがでん粉である。波が一段だけの一番見かける構造の段ボール(シート)を両面段ボールと呼び、波が二段になっている複両面段ボール、三段になっている三層段ボールというものもある。
さらに波の部分をよく見てみると波の間隔(密度)が大きいものと小さいものがあり、特に小さいものは「マイクロフルート」と呼ばれ、一見しただけではただの板紙にしか見えないが、同じ厚さなら、マイクロフルート段ボールは板紙とは比較にならない強度を持っている。
(1)段ボールの貼合
中芯とライナーを接着することを貼合(てんごう)と呼び、接着剤であるでん粉糊を調製することを製(せい)糊(こ)と呼ぶ(段ボールの業界は独特の用語が多く、知らない人が聞いていると内容がさっぱり分からないことがある。よって文中には〜と呼ぶが頻発する)。段ボールは「コルゲートマシン(図5)」と呼ばれる装置で波型に成型した中芯の段頂にでん粉糊を塗布し、まず裏ライナーと接着させ(シングルフェーサー,S/F)、次に表ライナーを接着させる(ダブルバッカー,D/B)。シングルフェーサー側は瞬間接着であり、熱ロールで圧力と熱を加えて接着させる。その後数十秒養生した後、ダブルバッカー側の接着を行う。ダブルバッカー側は熱盤の上を通らせることで接着と乾燥を行い、シングルフェーサー側の完全乾燥も同時に行う。
(2)段ボールの製糊
製糊方式は大きく「ツータンクシステム」と「ワンタンクシステム」に分けられ、ワンタンクシシテムはさらに「スタインホール法」「プレミックス法」「ホウ酸添加反応法」などがある。このシステムにおける段ボール用の糊剤は独特であり、キャリアと呼ばれる糊化させた糊液部(キャリア部)と、メインと呼ばれる未糊化でん粉部(メイン部)で構成され、糊剤はでん粉糊液中に未糊化でん粉が分散している状態である。また構成成分はでん粉だけではなく、粘度調整および未糊化でん粉の沈降防止のためにホウ砂(しゃ)が添加され、糊化温度のコントロールのために苛性ソーダも入り、耐水性が必要な場合は耐水化剤が添加される場合もある。
ツータンクシステムはキャリア部を作製した後、別タンクに用意したメイン部(でん粉スラリー)に混合する方式であり、ワンタンクシステムはこれを一つのタンクで行うことになる。
(3)キャリア部とメイン部
キャリア部はアルカリ(苛性ソーダ)によって完全に糊化されており、段ボール糊剤では極めて重要な役割を果たす。その一つはメインでん粉の沈降を抑え、適正な粘度を持たせることであり、キャリアがないとメインでん粉が沈降し、糊剤が不均一となり、適正な粘度がないと糊ロールにうまく乗らなくなる。もう一つの大切な役割は保水力の付与であり、でん粉糊剤に保水力がないとライナーや中芯に塗布したと同時に水分が紙側に吸われてメイン部の未糊化のでん粉が膨潤、糊化するのに十分な水分が足りなくなり、接着不良となる。またキャリアでん粉を糊化させるのに使用したアルカリは、メインでん粉の糊化温度の調整の役割も果たす。
メイン部の未糊化のでん粉は接着剤としての主役であり、キャリア部の助けとコルゲートマシンの熱(と加圧)によって糊化することにより接着力を発揮する。メイン部のでん粉はキャリア部から供給されるアルカリによって糊化温度がコントロールされる。一般的に糊化温度が低いほど、糊化に必要なエネルギーも下がりコスト的に優位であるが、現実的には糊化温度を下げ過ぎると操業上のトラブルが各種発生するため、そのマシンに合わせた糊化温度が設定される。
(4)接着のメカニズム
基本的な接着のメカニズムはシングルフェーサーもダブルバッカーもほとんど同じであり、界面接着、浸透接着およびでん粉の凝集(ぎょうしゅう)接着の複合であるが、接着の条件はかなり異なる。シングルフェーサー側は界面接着(およびでん粉の凝集接着)が主となり、瞬間的な加圧と熱だけで、ダブルバッカーで完全接着させるまでの初期接着力を発揮させる必要がある。接着力はショルダーと呼ばれる部分が主に担当する(図6)。ダブルバッカー側は浸透接着(およびでん粉の凝集接着)が主となり、ほとんど加圧は行わず密着程度の圧力でシングフェーサーより低温、長時間(数秒)で接着を行う。シングルフェーサー側の最終的な接着力は、ダブルバッカーの熱で乾燥することにより発現する。
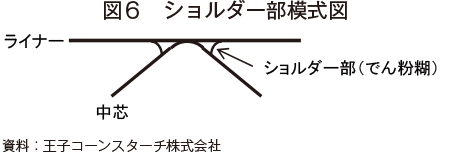
参考文献
王子製紙編『紙の知識100』東京書籍
王子製紙編『紙パルプの実際知識』東洋経済新報社
高田直屹『製紙工業』大日本工業学会
五十嵐清一『段ボール包装技術入門』日報
『段ボール実務知識』一律書房
このページに掲載されている情報の発信元
農畜産業振興機構 調査情報部 (担当:企画情報グループ)
Tel:03-3583-8713